Focusing strongly on people development, raising client levels of education and awareness of supply chain strategies, SSM Group conducts complete assessments of the supply chain itself, as well as assessments of logistics elements within the supply chain. According to the requirements of the client, stages of the consulting process can be conducted in isolation, or as a wide ranging package of services.
SSM Group’s Professional Advisory Services take into account the hands-on nature of the supply chain world. While backed by leading edge technology, SSM Group engages with clients in a personal environment, and on all levels – from physical visits to warehouses and brown paper assessments to technology driven supply chain re-design.
People are a key element of SSM Group’s Professional Advisory Services offerings. A thorough skills-gap assessment and the formulation of a people development programme form an intrinsic part of our consulting process.
People, Processes & Technology
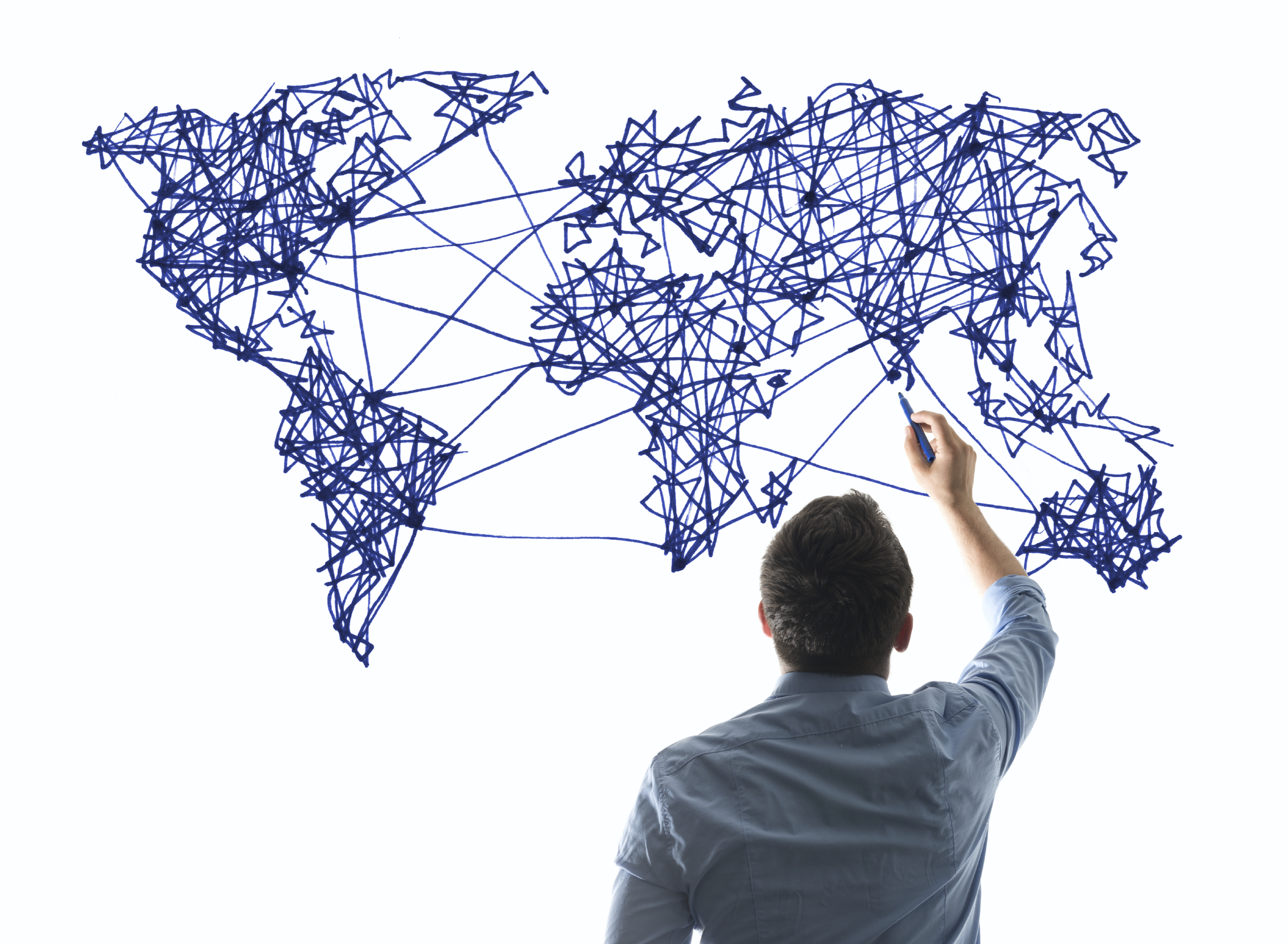
There are many constituent parts that make up an effective supply chain. The advisory process can be conducted with a focus on distinct areas of the supply chain, or it can focus on the logical analysis of all the elements within the chain.
Professional Services
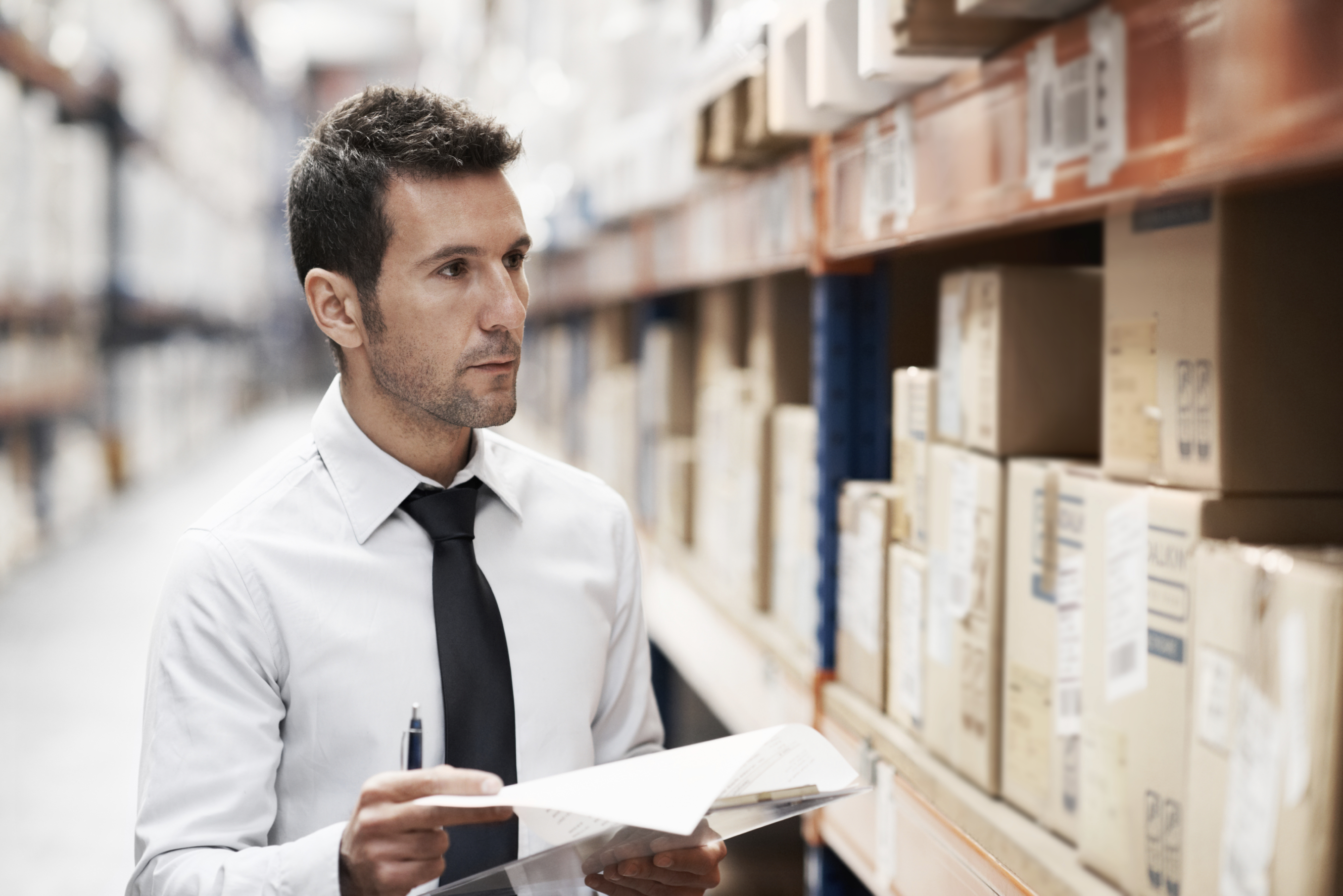
Assessment and Evaluation of Supply Chain Performance
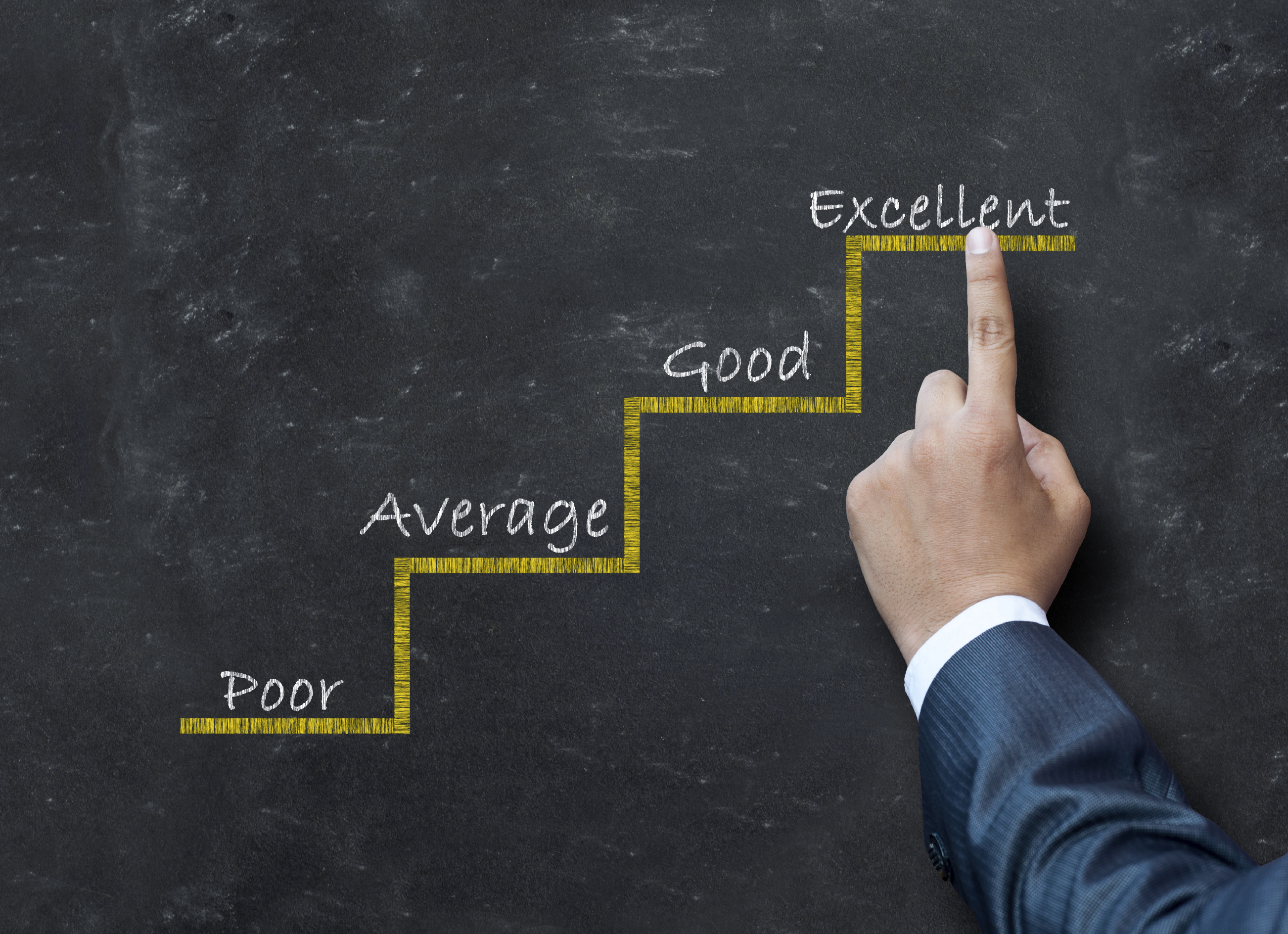
- Supply Chain Evaluation:
– Alignment with Business Objectives & Customer Service
– ‘Best Practice’ Comparative Benchmarking
– Service Performance
– Cost Ratios
– Operational Performance
– Agility & Responsiveness
– Future Capability - Environmental Carbon Footprint Assessment
- Cost Structure and Customer Profitability Reviews
- Supply Chain Planning and Inventory Assessment
Assessment and Evaluation of Supply Chain Performance
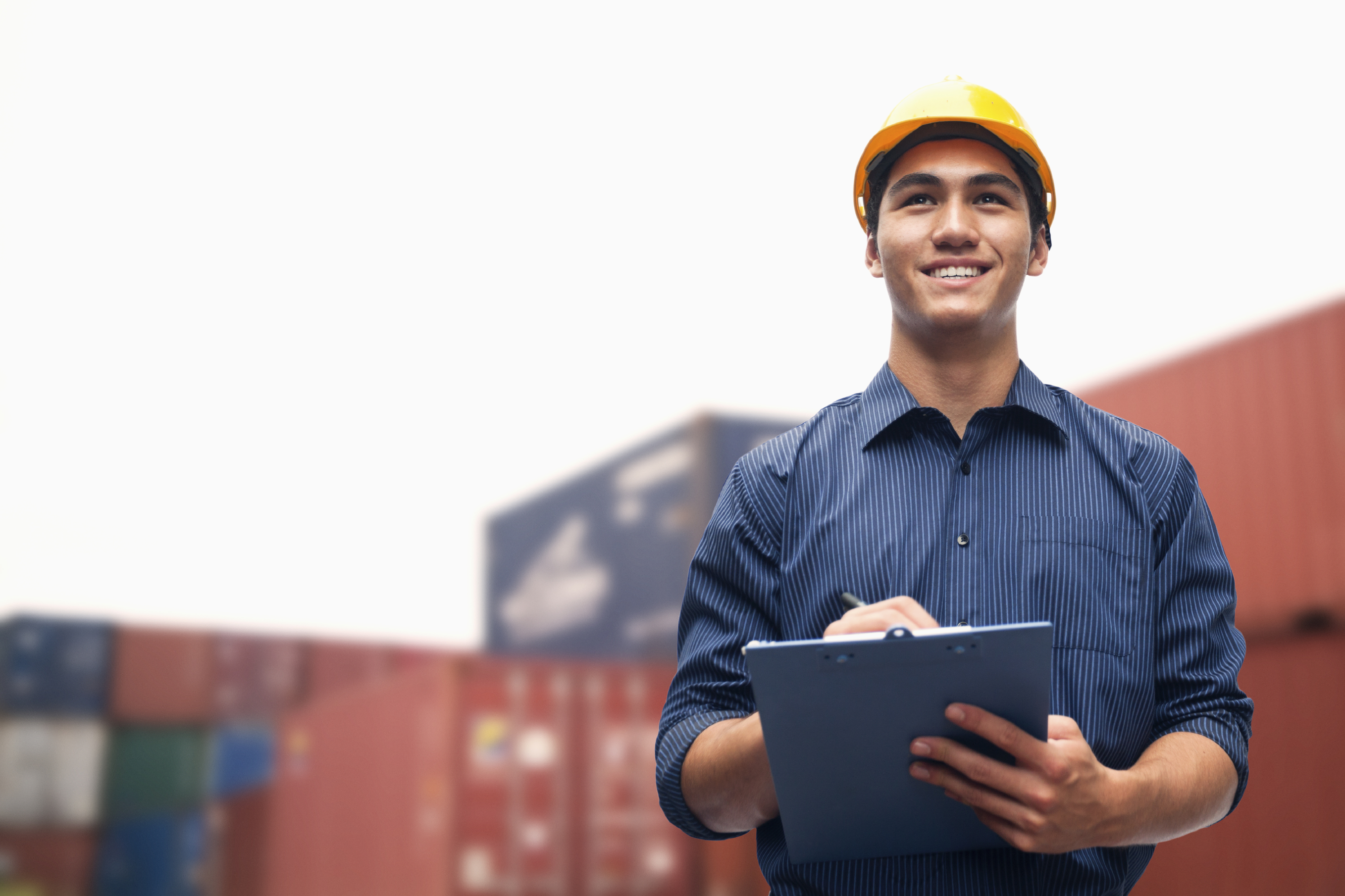
Supply Chain Strategydeveloping the vision taking into account:
- Business Objectives
- Sales and Marketing Strategies
- Customer and Retail Service Requirements
- Sourcing and Procurement Policies
- Manufacturing Capabilities and Strategies
- Environmental Policies
- IT and Finance Issues
Modelling the Supply Chainwith expertise in:
- Business Process Mapping
- Strategic Modelling from Sourcing to Customer
- Network Design
- Distribution & Warehouse Modelling
- Inventory Planning
- Carbonfootprint modelling
Environmental Strategies and Implementation
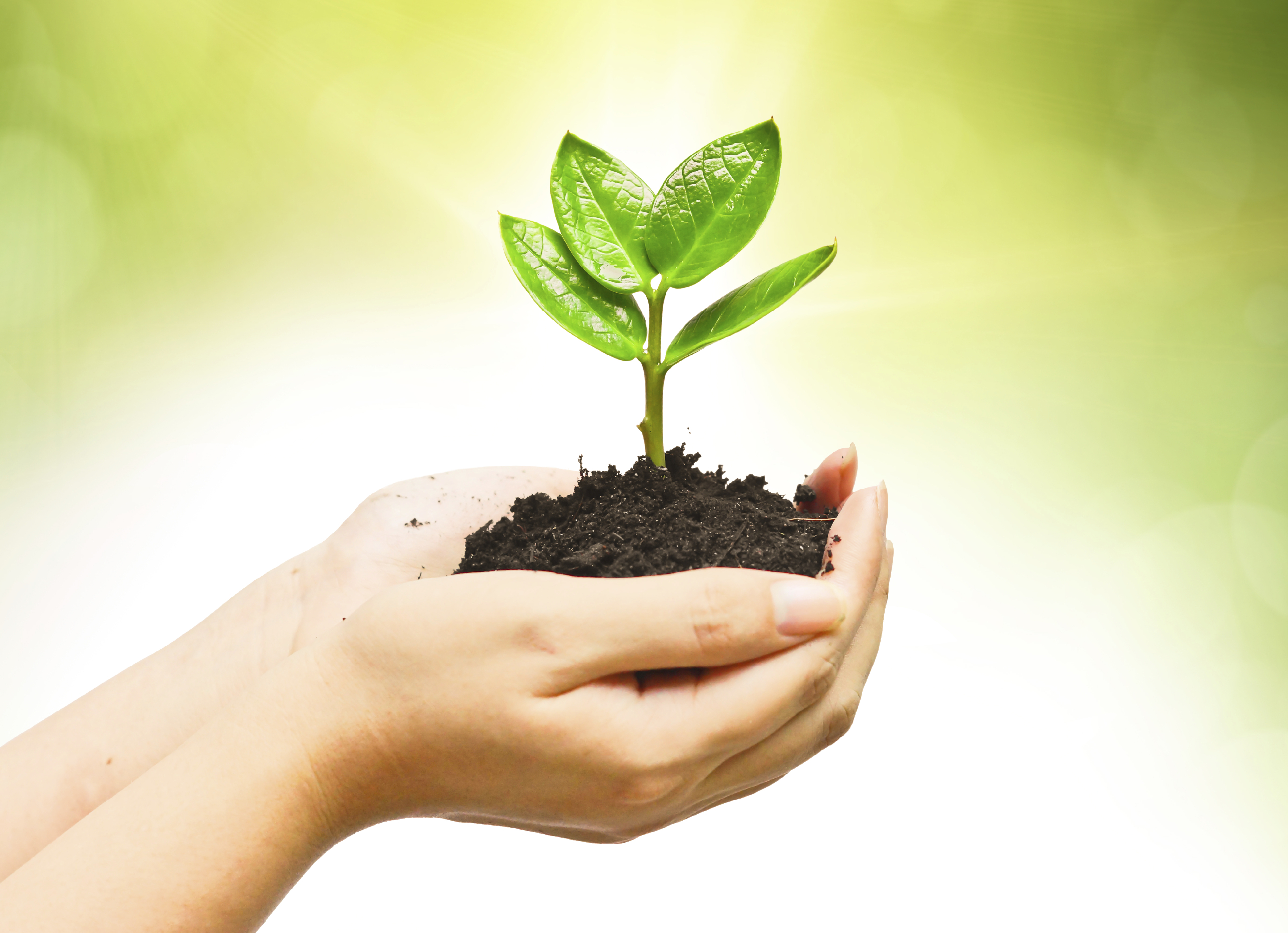
Distribution Centre Design and Operations
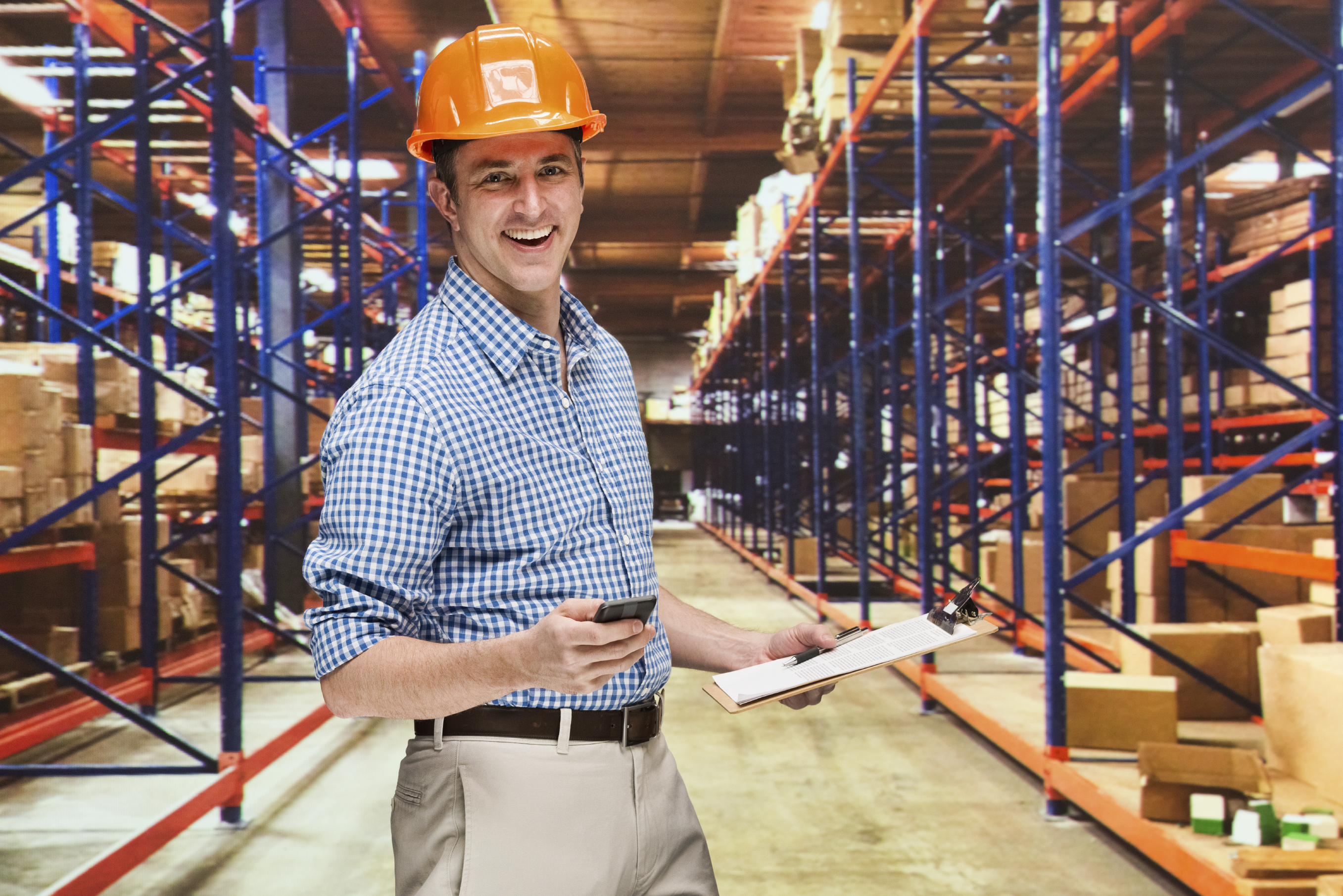
- Existing Warehouse Re-design and Re-organisation
- Minimising Environmental Impact
- Automation and MHE Assessments
- Picking & Sortation Systems
- Staffing Arrangements
- Computerised Simulation
- WMS Systems Expertise
- Audits and Performance Assessment
- Benchmark Comparisons
- Greenfield Warehouse, Layout and Operations Design
Transport Planning & Scheduling
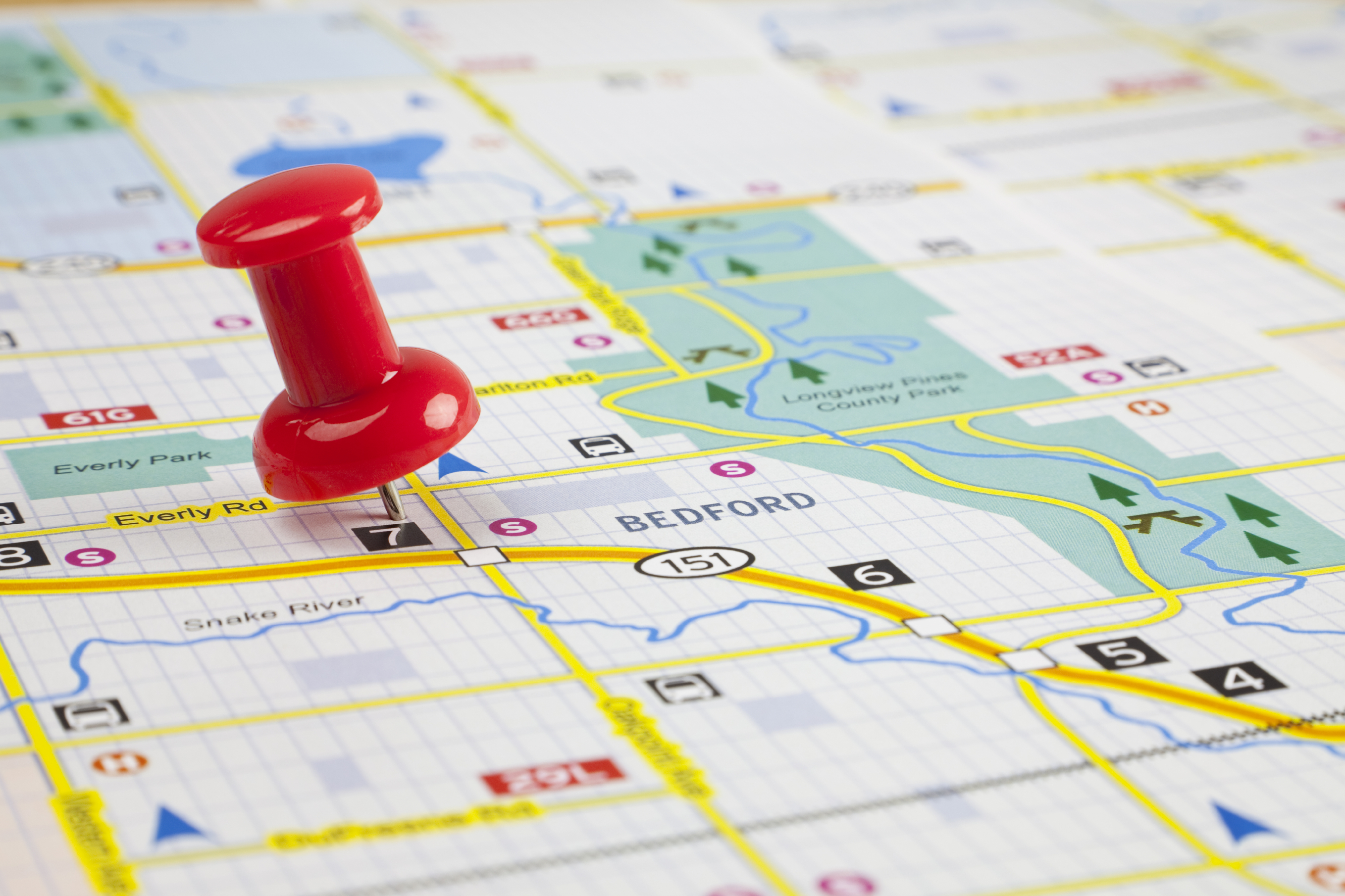
- Routing and Scheduling
- Network Re-structuring
- Fleet Requirements
- Environmental Impact of Fleet Structure and Operations
- Driver Staffing Arrangements
- Fleet and Carrier Management
- Back-load and Haulier Assessment
- Working Time Directive
- Fuel Efficiency
- Audits and Performance Assessment
- Benchmark Comparisons
Contract Logistics and Outsourcing
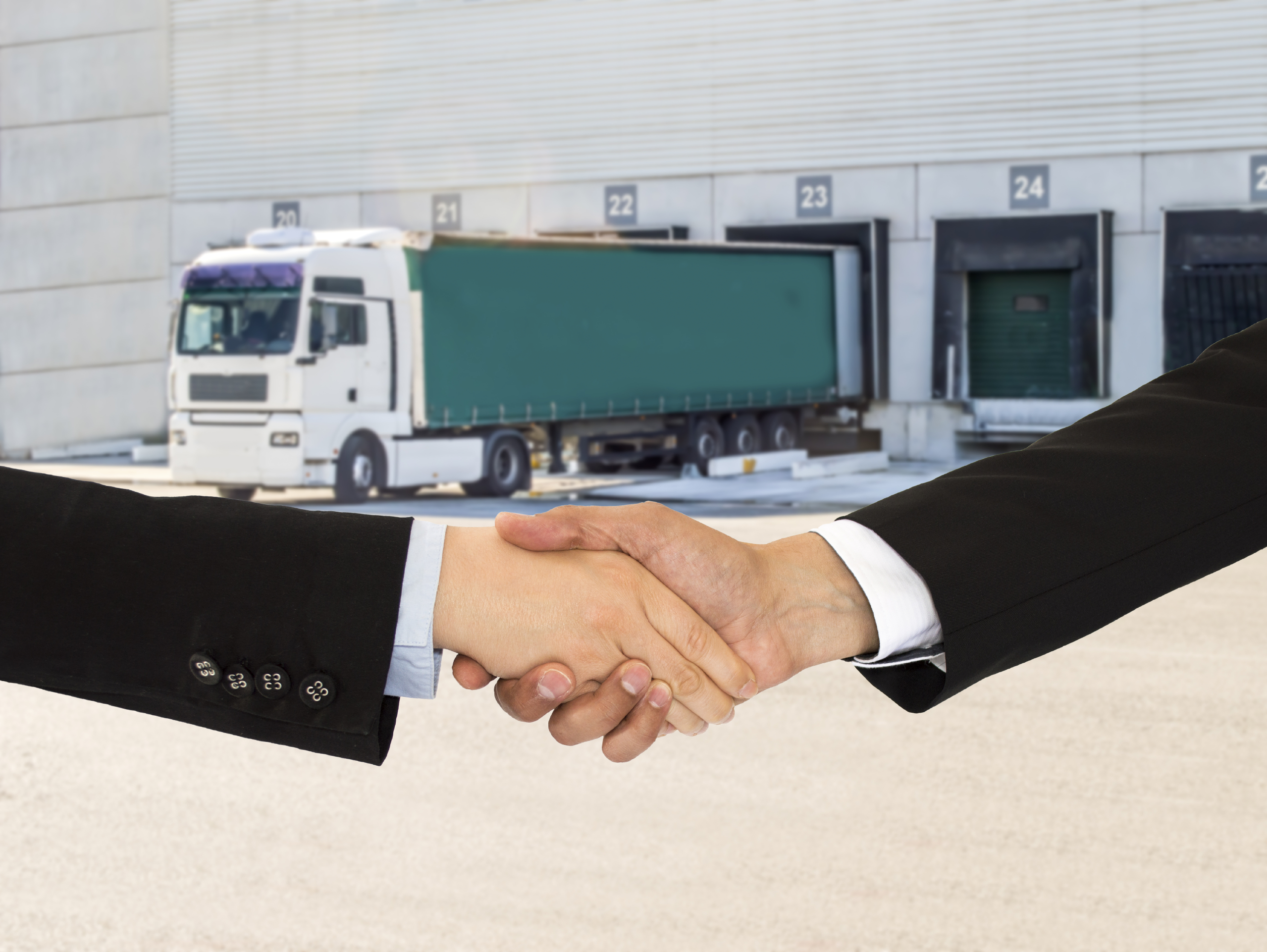
Assessment and Evaluation of “In House” versus “Contracted” options:
- Contractor comparisons
- Tendering and Selection Process Management
- Negotiation and Contract Arrangements
Contract Implementation:
- Contract Performance Reviews
- Monitoring, Auditing and Benchmarking
Logistics Provider Support Roles:
- Contract Bid Evaluations
- New Contract Implementation
- Current Operations Management
- Strategic Business Evaluations
- Business Development Initiatives
Inventory & Planning Management
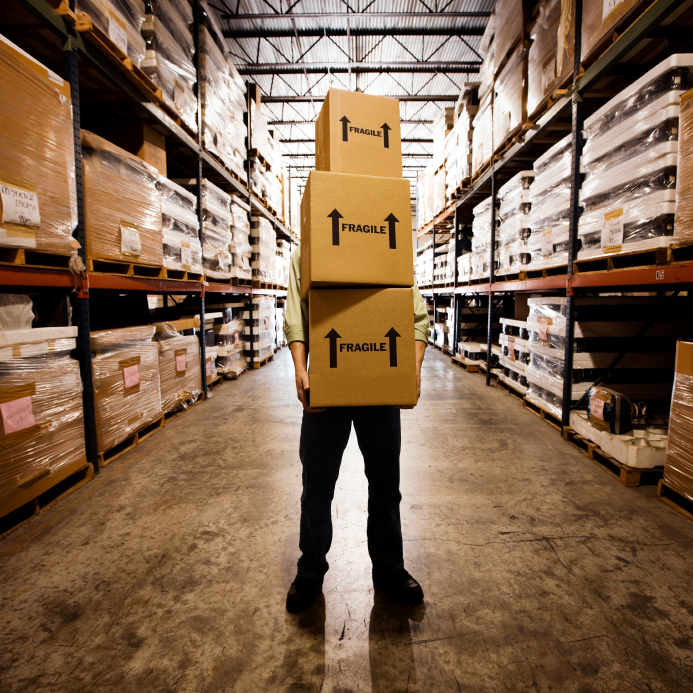
- Business Process Mapping
- Demand and Supply Forecasting
- Procurement Policies
- Inventory Management
- Promotions and Sales Fluctuations
- Supplier Reliability
- Lead Times and Stock Availability
- Vendor and Co-Managed Inventory
- Inventory Simulation
- IT Systems Selection
Management and Successful Implementation of Change
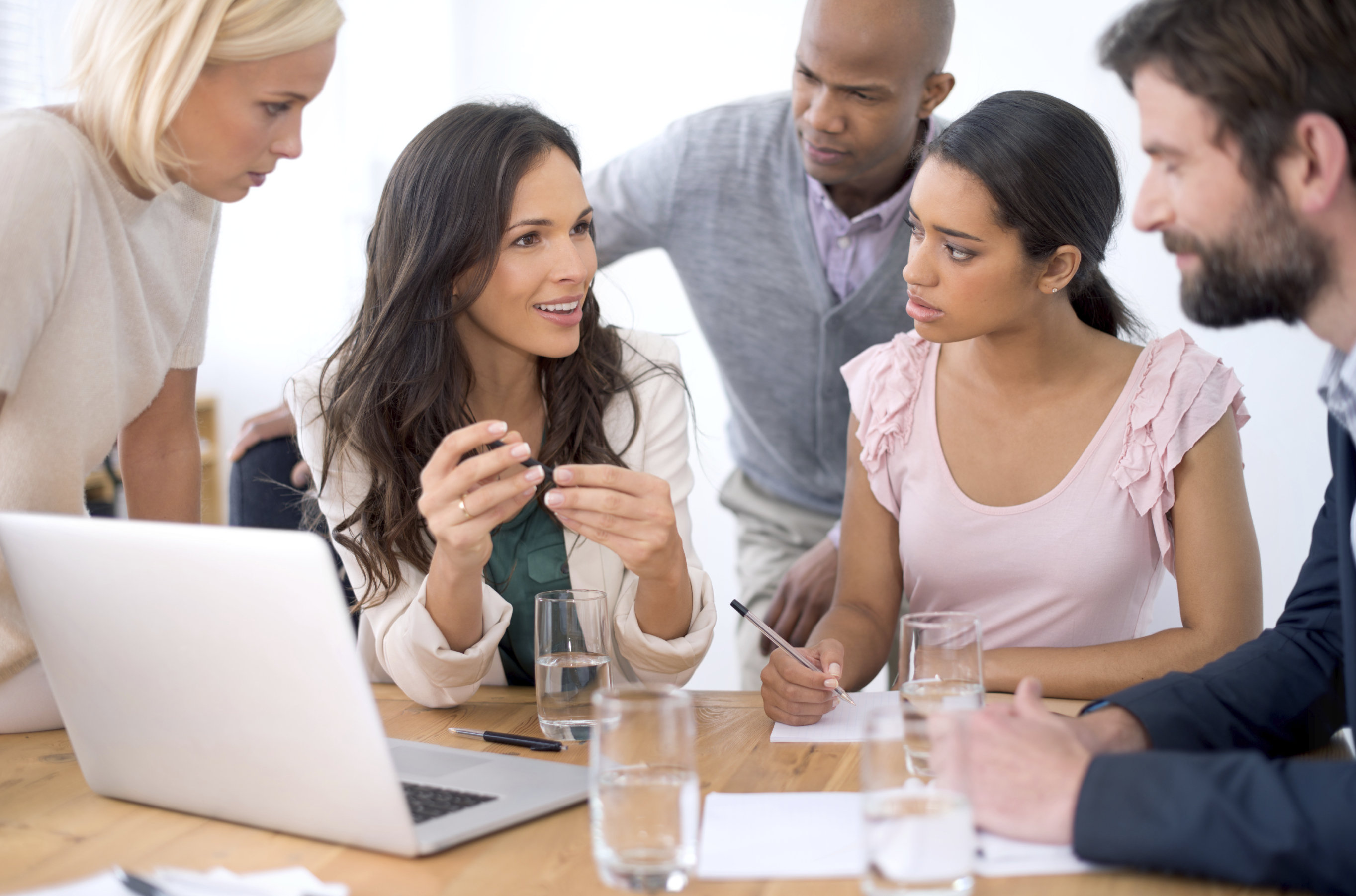
- Project Structuring
- Detailed Planning and Timetabling
- Risk Assessments
- Budgetary Controls
- Communications Management
- Installation and Fit-out Management
- Staff Training
- Changeover Co-ordination
Interim Management
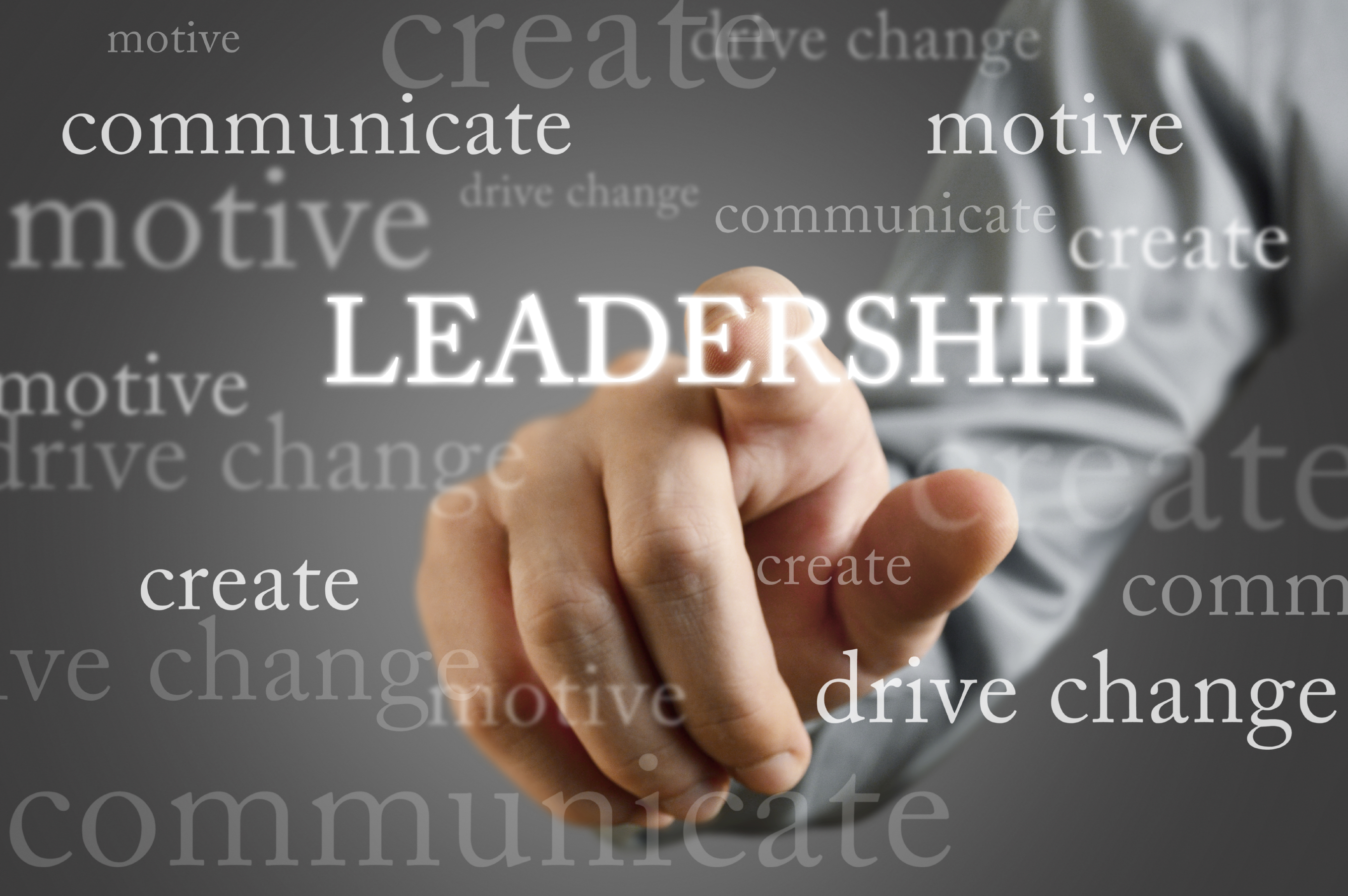
- Highly Experienced Managers and Directors
- Strong Logistics Management Backgrounds
- Minimal Start Up and Learning Curve
- Good Communicators and Project Controllers
- Expertise in Change Management
- Excellent Capability to Manage Crisis Situations